Bateau léger
Cette catégorie représente les navires de transport de passager. Lors de la compétition, chaque bateau est chargé de lests de 20 kg.
2019 - Construction de foils
En 2019, l'objectif de l'équipe de mettre des foils sur le bateau léger construit l'année précédente. Nous utiliserons la technologie des foils autostables.
2018 - Fabrication d'un nouveau catamaran
Pour le concours 2018, l'équipe a construit un nouveau bateau léger. Notre catamaran est composé de plaques de contreplaqué marine que nous avons assemblées. Il mesure 2,5 mètres de long.
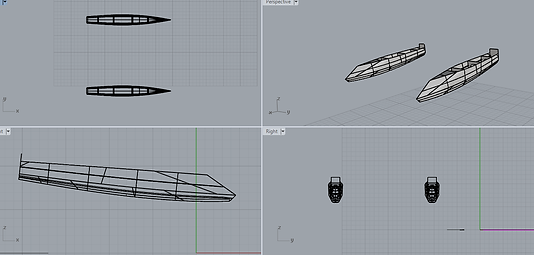
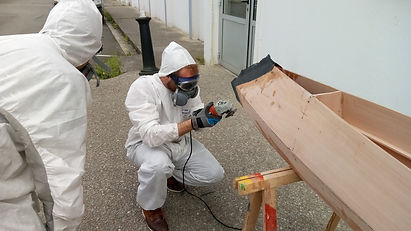
Création d'une étrave renforcée en carbone
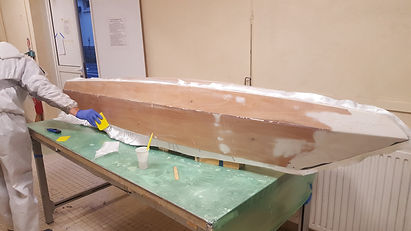
Pose de fibre de verre stratée
2016 - Bateau éco-conçu

Le bateau léger a été réalisé dans une optique de bio-conception.
Il est ainsi construit en fibre de lin, avec résine thermoplastique.
Les deux flotteurs ont été faits à partir de moules en argile imprimés en 3D.
Un énorme merci à nos partenaires pour leur aide et leur soutien tout au long du projet et de la construction !
Le bateau léger a terminé 2ème du concours en 2016!
La Construction en images
![]() Infusion_1Le moule est une ancienne coque. | ![]() Infusion_2Mise sous vide du moule et de la fibre. | ![]() Infusion_3C'est parti pour l'infusion ! |
---|---|---|
![]() Coque_1Il faut coller les deux parties maintenant. | ![]() Coque_2... et coller la plage arrière. | ![]() coque_3Tadaaaa ! |
![]() Flotteur_1Moule argile des flotteurs | ![]() Flotteur_2Strate sur le moule. |
Le dossier Prix Eco-Conception
When it comes to energy efficiency, we think about ways to use less energy while the ship is in function. What cannot be put aside is that it represents just one part of the boat's life. The entire product life cycle must be a point of reflexion.
Is the material recyclable? If not, what will it become? Is the process safe and not polluting?
As future engineers, it will be our responsibility to integrate it in our thoughts and to act for ecodesigning.
How did you organize yourselves to make ecodesign happen?
We thought about eco-design at the very beginning of the design stage. We visited Kaïros Composite in August 2015 in order to present our project and see how we could integrate eco-design in it.
The first idea was to design a new hull, we finally decided to keep our former hull which we used as a mold. This non-standard technic allows to produce less waste.
Our sponsors gave us all the materials we needed, and we were then able to do the infusion in one phase.
Where are the main environmental impacts of your project?
We did not realize it before, but the infusion has a huge environmental impact. We generated 17 kg of waste for half a hull. A part of it was the resin that had thermal runaway. Luckily, because we used a thermoplastic resin, most of the boat will be recycled as plastic. Because of the thermal runaway, the raw finish at the end of the infusion was not great.
Thus, we looked for different solutions to have a smooth finish. We finally found a solution that will not contaminate the boat and make it non-recyclable: we applied a removable paint (plastidip). This paint will also ensure that the boat is watertight.
The second main impact is the glue we had to use. We tried several times to glue the two parts of the boat with a similar chemistry as the resin but the glue was reacting with air. We finally had to use epoxy glue, which is not recyclable but we can still cut around the region in contact to recycle most of the boat.
The third one is due to a lack of time. We didn’t have extra time to make a lax balsa core composite plate for the back plate of the boat. Instead it a fiber glass reinforced wood panel. It the same as the glue, we will cut it before recycling.
What are your main actions and achievements?
The use of a thermoplastic resin was a big part of our work. While using this resin, we had to accept not to use standard technic of finish (gloat, primer or epoxy paint).
The fiber we used is lax for the hull and jute for the floats. To reinforce the main hull, we used balsa core. The lax fiber and balsa core were found around us (Kairos Composite and Sicomin). For the recyclable resin, it came from south of France (Arkema).
The resin and jute for the float are from the UK because of time constraints (easycomposite). The resin for the float is partially bio sourced (37 % SuperSap CLV ). We wanted to keep the cost down so this was a good balance.
Using our previous boat as a mold made finally a lot of sense because it allowed us to generate less waste. We also did not use a gel-coat for demolding from the “mold”. We experimented a lot with elastic film in order to “put in a bag” the old hull. The main advantage of the elastic film is that it did not make too many defaults because it stretches a lot. This also prevents the resin from sticking to this one. The other advantage of this film was to try to use less film to cover the boat.
Thanks to our partner Diatex, we pick the right product. We also exchange about the reusable products from their catalog we could use. Unfortunately, it is not compatible with the infusion technic.
However, in the long term, this solution is not viable. So for the float, we partnered with a concrete and clay 3D-printing company from Paris (xtreee) to develop a technic that allows us to a recyclable mold.
The build of the floats is planned for June, 9th. The plan is to 3d print the shape of the float in clay. Then we apply a coat of wax with a machine developed in house. This will allow us to have a perfect finish on the "master". Then we will apply the fiber directly on the wax. When all is dry, we dissolve the clay part and heat the wax to melt it. The only waste will be the wax, contained by the clay and resin. The 3D-printing head is mounted on a robotic arm so we are not limited by the size of the "printer". If it a success, we could use it for the next boat. The development of the technic is a big step to try to achieve better eco design boat.
We finish the test this last week-end. There are plenty of pictures now. The clay was easily removed by adding some water. After few hours the clay is liquid. The finish is quite good. We are really excited by the result.
What are the main innovations and lessons learned?
The boat is near to fully recyclable. We have plenty of ideas to go further. For the next edition, we will experiment even more.
Our partners are ready to move forward and we will work with them. They have already provided us a lot of advice. We are only at the beginning of the industrialization of eco-friendly boast. It is really challenging and we would like a lot to experiment and to push further this technology. It fits perfectly with the spirit of the Hydrocontest competition.